
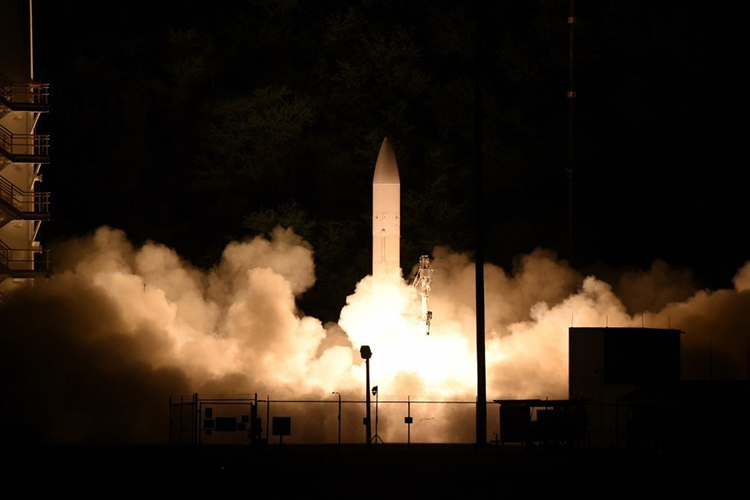
Flying High in Aerospace
For decades, aerospace manufacturers have been incorporating composite components into their aircraft to cut back on weight, save on fuel and reduce the environmental impact of commercial, business and military flights. With the development of new technologies, composite materials will play an even bigger role in the aircraft of the future.
The work on composites for aerospace is continuing on many fronts, three of which are highlighted in this article. At a new technology hub in England, aerospace engine manufacturer Rolls-Royce is showcasing automated production of composite fan components. In Wichita, Kan., Spirit AeroSystems is finding ways to improve the properties and production of composite materials designed for hypersonic flight. And in Florida, university researchers have significantly increased the strength of 3D-printed composite materials, making them better candidates for structural components of aircraft.
New Methods of Production
More sustainable, more automated production of composite materials could lead to their increased use in the aerospace industry. Rolls-Royce’s new composite technology hub in Bristol, England, provides a possible model for future manufacturing. Opened in January 2020, the facility is manufacturing CFRP fan blades and fan cases for demonstrator models of Rolls-Royce’s innovative UltraFan® engine. The UltraFan represents the first big architectural change in Rolls-Royce’s aircraft engines in several decades.
“UltraFan brings together a whole series of new technologies that combine the propulsive efficiency benefit of a large, low-speed fan driven through a power gearbox with a high-technology, high-speed and very power-dense, gas generator core,” says Andy Geer, chief engineer, UltraFan product development and technology at Rolls-Royce. This enables both fuel burn reduction and emissions reduction. “From a cost point of view and an environmental footprint point of view that is very much where the future of aerospace is pointed,” says Geer.
The company estimates that the incorporation of composite fan blades and fan cases will reduce the weight of the jet engine by more than 1,500 pounds, the equivalent of seven passengers. Overall, UltraFan will deliver a 25% reduction in fuel burn and CO2 emissions compared to Rolls-Royce’s first Trent engine family member.
Rolls-Royce partnered with the United Kingdom’s National Composites Centre on the development of UltraFan’s composite fan components. The initial work was done at the company’s academic-style research facility on the Isle of Wight. The next stage will happen at the composite technology hub, a pre-production facility that features state-of-the-art, automated manufacturing methods. The building is powered primarily by solar power and designed for sustainability with low-energy, very-low-emissions manufacturing processes.
“We paid a lot of attention to ensure that the composite lay down and consolidation are relatively low-temperature processes and that the outgassing, or the products that are released during the assembly process, are in no way harmful,” says Geer. Sustainability concerns also guided Rolls-Royce’s choice of materials for the CFRP components and its design of manufacturing processes that result in minimal waste material.
To manufacture the fan blades, Rolls-Royce builds up hundreds of layers of carbon fiber materials, pre-filled with a resin that increases its toughness. Toray manufactured the carbon fibers, which Hexcel Composites incorporates into the prepreg materials that it supplies. Rolls-Royce partnered with Delaware-based Accudyne to develop the specialized automated robotic systems that perform the material lay-up. The composite components are cured through the application of heat and pressure, and the blades are finished with a thin titanium leading edge to provide protection against erosion, foreign objects and bird strikes. Inspection systems are integrated throughout the process to ensure the quality of each part produced.
The factory’s pre-production technology can be easily scaled up to meet actual production demands, according to Geer. That’s especially important in the aerospace industry, where new aircraft components must go through rigorous qualification testing.
“Once you’ve achieved that certification, you have to be able to prove that the parts that you make subsequently are equivalent to those that were certified. So precision, accuracy and repeatability are a key part of that process,” says Geer. By controlling the manufacturing process, the company is able to demonstrate that the 100th part it builds will be made the same way and to the same quality standards as the first part it built. That’s harder to do when there’s a human factor involved, as in manual lay-up.
The fan blades and cases are not the only composite components on the UltraFan engine. Geer says that organic polymer matrix composites are used extensively throughout the fan system, and other composite materials are incorporated into the acoustic panels, into the infill for aerodynamic fairings and for the annulus (part of the engine combustion system). Ceramic matrix composites are being used in the hot sections of the engine.
Rolls-Royce plans to have the demonstrator model of its UltraFan engine completed by the end of 2021. While the company is in discussions with aerospace manufacturers about including the engines in new aircraft designs, COVID-19-related slowdowns in the industry make it difficult to predict when such projects will move forward.
“Our intent is to put a number of demonstrator engines through a pretty rigorous characterization and test program, prove that we understand the technology and that we’re completely ready to productionize it,” Geer says.
Standing up to Super Speeds
Hypersonic aircraft, used primarily by the defense and weapons industry, are designed to travel high in the earth’s atmosphere at speeds ranging from Mach 5 (about 3,800 mph) to Mach 20 (about 15,000 mph) or more. One of the biggest challenges in designing aircraft for these speeds is developing materials that can handle the effects of atmospheric drag.
A hypersonic vehicle must withstand temperatures ranging from around 1,200 degrees F to more than 4,000 degrees F in certain areas, depending on how fast the aircraft is traveling. “The ability of the materials and structure to react to rapid changes in temperature and to work properly when the vehicle experiences large temperature differences over various parts of the structure is absolutely essential,” says Chris Boshers, senior director and chief engineer of defense engineering at Spirit AeroSystems.
The structures that provide thermal protection for a hypersonic aircraft require high strength and stiffness because they also have to withstand the large dynamic pressures and g-loadings (forces of acceleration) of hypersonic flight. Composite materials can provide these properties, but those unidirectional fibers may suffer from delamination and premature failures.
“The strongest and most efficient temperature materials [for hypersonic aircraft] have fibers oriented in three directions to react to three-dimensional applied loads,” Boshers says.
To produce these hypersonic-ready composite materials, Spirit AeroSystems, which has expertise in material design and fabrication, recently acquired FMI, which has been developing and producing high-temperature composites for more than 50 years. The combined teams hope to improve the value proposition for hypersonic flight by making the required materials, and thus the aircraft, more affordable, more efficient and producible in quantity.
Spirit is working with two different types of composite materials for hypersonic applications – carbon/carbon and ceramic matrix. Carbon/carbon (C/C) composite materials can maintain high strength at temperatures above 4,000 degrees F while also retaining a predictable aerodynamic strength. In hypersonic aircraft, C/C composites are used for nose tips, control surfaces, thermal protection systems (TPS), aeroshell applications, and the nozzles and throats of rocket motor exhaust systems. Other potential applications include TPS for space re-entry vehicles, heat shields and high-temperature engine components, as well as oven walls and high-temperature probes for industrial applications.
To produce C/C composite parts, Spirit weaves tows of carbon fiber, each consisting of bundles of thousands of individual carbon fibers, into three-directional arrangements of straight or uncrimped fibers.
“After quality assurance inspections ensure the fiber architecture is correct, then heated, pressurized pitch is forced into the spaces between the fibers,” Boshers explains. “Following this infusion process, the billet is heated to char the pitch, leaving only carbon behind. The infusion process is repeated multiple times to fill up any remaining voids, resulting in a very dense, very uniform block, or billet, of carbon-carbon.” The company can mill multiple aircraft components from a single billet.
Spirit is working to automate the C/C manufacturing process to reduce labor costs and improve product quality, to accelerate the densification process and to produce near-net shape components. Boshers says those changes could improve the buy-to-fly characteristics of the C/C material, making it more affordable.
Spirit is also developing ways to make production-scale quantities of ceramic matrix composite (CMC) materials for hypersonic vehicles. CMCs maintain strength and stiffness like C/C composites, but operate at a lower temperature range of 1,500 F to 2,200 F. CMCs do have better environmental resistance, especially to oxidation, than C/Cs. They can be used for components in non-peak-heat areas of aircraft, for some thermal shielding and for scramjet inlet ducts.
Spirit’s CMC materials include either carbon, silicon carbide (SiC) or aluminum oxide (Ox) fibers. With the carbon and silicon carbide fibers, the company uses silicon carbide as the matrix material. Aluminum oxide fibers are used with an aluminum oxide matrix.
To perform the specialized, high-temperature testing (up to 5,000 F) of both C/Cs and CMCs, Spirit has built its own energy materials testing laboratory. It is also partnering with the National Institute for Aviation Research (NIAR) on construction of a high-temperature materials test facility in Wichita. “This facility will provide the capability to characterize high-temperature C/C and CMC materials, and provide certified B-basis statistical allowables for the design of hypersonic vehicle structures,” says Boshers. (B-basis is the strength value at which only 10 in 100 specimens will fail with a 95% confidence level.)
Boshers sees many additional opportunities for composite materials in the hypersonic market. “We are exploring new fiber architectures and materials that offer cost/performance benefits in hypersonic applications,” he explains. “Near-net shape materials, larger size components to reduce or eliminate joints, and materials that can more effectively resist ablation or erosion are currently being developed. Longer term, the use of high-temperature-resistant, durable materials could be used in jet engines to reduce weight and improve efficiency, resulting in reduced fuel use and lower CO2 emissions.”
Although the defense industry has been the biggest customer for hypersonic aircraft materials, there is growing interest from the commercial sector as well. Companies like SpaceX and Virgin Galactic are developing technologies that will slash the time it currently takes to transport both passengers and cargo around the world. Composite materials will play a key role not only in the development of these hypersonic aircraft, but also in the production of many other innovative future aircraft.
3D-Printed Aircraft Components
Additive manufacturing (AM) of composites enables quick production of components of almost unlimited geometries with very little waste. But most AM work today is done with thermoplastic materials, which don’t have the properties necessary for aircrafts’ structural components. Thermoset composites made with carbon fiber can provide the required strength and durability, but incorporating carbon fibers into the printing mixture has been problematic. When the carbon fiber count gets too high, the fibers clump together and clog the nozzle of the 3D printer so that it can’t print.
Emrah Celik, assistant professor of mechanical and aerospace engineering at the University of Miami, has developed a process that solves this problem. He found that vibrating the carbon fibers at the printer’s nozzle prevents them from clumping and allows the printing process to proceed.
In the course of working on AM projects for NASA and the Air Force, Celik was able to customize off-the-shelf, 3D extrusion printers to produce carbon fiber thermoset parts. In 2019, Celik and his Air Force research partners published a paper describing how they had been able to manufacture a thermoset part with about 6% carbon fiber by volume. “That was great at the time, and we exceeded what was state-of-the-art practice,” he says.
But Celik wanted to add more fiber to produce even stronger composite components. With his graduate assistant, Nashat Nawafleh, he explored several variables, including the optimal length of the carbon fibers, the surface treatment of those fibers and the impact of different levels of vibration on the thermoset material.
With vibration, for example, “You don’t want to vibrate too much, because you don’t want to reduce your resolution or change the dimensional accuracy,” Celik says. “But the vibration has to be the right amount to separate the fibers from each other so they don’t clog the nozzle.”
After experimenting with Kevlar® and glass fibers, Celik focused on carbon fibers because of the strength they provide to the composite material. He initially worked with chopped carbon fibers about 6 millimeters in length, but eventually chose milled carbon fibers approximately 50 microns long. After testing a variety of surface chemistries for these shorter fibers, Celik found that sized materials provide the best linkage between the resin and the carbon fibers.
In thermoplastic AM, the bonding between layers of a composite may not be strong because the material is heated up for printing and quickly cools down. Celik’s thermoset AM process delivers a more isotropic result; the printing “ink” is composed of nanoclays or silica, mixed with a thermoset resin and then with the carbon fibers right at the nozzle. “It becomes a gel type of material, and when you extrude it on a surface it has enough strength to keep its shape,” he explains. The gel in each layer fuses well to the layer underneath, and when the part is completed, it is put in an oven to cure overnight.
The isotropic properties are also improved because of the use of the shorter carbon fibers. During the extrusion process, the fibers in the printing ink tend to align in the direction of the printing, reducing the strength in other directions. Since the shorter fibers don’t align as much as longer ones, the thermoset composites in Celik’s process show 80% strength in the transverse direction.
With all of these changes, Celik realized an impressive improvement in the carbon fiber content of the printed thermoset composite. “Instead of 5% to 6% fiber, we could now fabricate materials with 46% carbon fiber by volume,” he explains. The material is as strong as metal, but 80% lighter than steel and 50% lighter than aluminum.
Celik believes the lightweight thermoset composite parts produced through this AM process will be able to replace heavier metal components. In addition, with 3D-printed composites, aircraft manufacturers could re-engineer components. Only the parts that require structural integrity have to be solid; in other areas, honeycomb configurations could be used to further reduce an aircraft’s weight.
Several Department of Defense agencies have already expressed an interest in Celik’s work. While aerospace may be the first industry to use the technology, he sees additional applications in transportation and other industries, especially if the cost of producing carbon fiber can be reduced.
From 3D printing to advances in materials, the variety of R&D going on today reflects the many possibilities that composites offer for aircraft and spacecraft of the future.
SUBSCRIBE TO CM MAGAZINE
Composites Manufacturing Magazine is the official publication of the American Composites Manufacturers Association. Subscribe to get a free annual subscription to Composites Manufacturing Magazine and receive composites industry insights you can’t get anywhere else.