
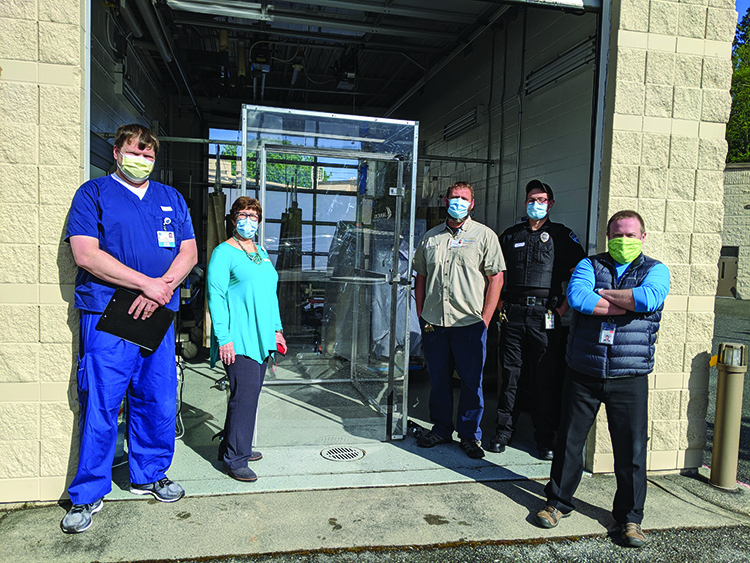
Good Neighbors
Skagit Valley is an idyllic region in northwestern Washington, renowned for its tulip fields and berry farms in the south and the breathtaking peaks of the
Cascade Mountains in the north. It’s also home to dozens of close-knit communities where neighbors take care of one another. That compassion has been on display during the COVID-19 pandemic, with more than 400 Skagit County residents testing positive for the coronavirus as of mid-May.
Janicki Industries, a fourth-generation, family-owned business in Sedro-Woolley, Wash., has a long history of giving back to the community. Local children play baseball and softball at the Janicki Fields, and the company supports groups such as the Rotary Club, Boy Scouts and United Way. So when Janicki Industries began getting requests to make equipment for the fight against COVID-19, it was a “natural fit” to lend a hand, says Andy Bridge, vice president of industrial and emergent markets for Janicki. The company designed and fabricated portable isolation treatment booths and intubation boxes for two local hospitals. “We are good at designing, engineering and manufacturing big components, like airplane wings and wind blades,” says Bridge. “So when hospitals wanted big boxes, we thought, ‘OK, this is in our wheelhouse.’”
Janicki Industries is one of many companies in the composites industry that has stepped up during the global pandemic to provide devices, personal protective equipment (PPE), hand sanitizer and more. “Manufacturers are resilient and agile,” says Lori Miles-Olund, president of Miles Fiberglass & Composites, which has made and donated face shields. “They can quickly answer the call for what is needed, and we have seen this during the pandemic.”
Keeping Caregivers Safe
One of the calls Janicki received was from Connie Davis, MD, chief medical officer of Skagit Regional Health Clinic, who sought a better way to isolate COVID-19 patients from healthcare staff during nebulizer treatments to deliver oxygen. She provided a sketch of an isolation booth to Janicki on April 9. Bridge initiated a design contest among the company’s engineering team, challenging them to submit viable designs using off-the-shelf materials within three days.
Bryan Harris, program manager, won the contest with a 4-foot-wide, 4-foot-long, 8-foot-tall booth, including a sealed door that could accommodate wheelchairs. The booth is made of clear polycarbonate so hospital staff can easily monitor patients. It features a ceiling fan with a high-efficiency particulate air (HEPA) filtration system. The 0.3 micron HEPA system creates a slight vacuum in the booth, preventing air from escaping and potentially transmitting the coronavirus to others.
On April 21, Janicki delivered the isolation booth to Skagit Regional Health Clinic. Subsequently, it fabricated a second booth for PeaceHealth United General Medical Center in its hometown. The company has no plans to mass produce the booths and ship then nationwide. Instead, Bridge shared an open source COVID patient isolation box design on his LinkedIn page, hoping others will produce booths for their local hospitals. “That would be the best reward for us,” he says.
In addition, Janicki has teamed with one of its customers, Eddyline Kayaks, to fabricate a handful of intubation boxes for Skagit Regional Health and PeaceHealth. The 3 x 3 x 3-foot boxes made from clear polycarbonate are used during patient intubation, when an endotracheal tube is inserted in the airway to assist with breathing.
The boxes, which fit around the head and shoulders of patients, feature two holes on the top where healthcare personnel insert their arms to perform the procedures. They help prevent respiratory droplets laden with a high viral load from spreading throughout the room.
Supporting Grassroots Efforts
Hexion Inc., a global provider of thermoset resins based in Columbus, Ohio, is another company that has tapped into the expertise of its 4,300 employees worldwide to provide solutions locally. “We want to be good neighbors in the communities we work in,” says George Knight, acting CEO and CFO of Hexion. “What I like about our initiatives surrounding COVID-19 is that they are all grassroots efforts. The ideas came from our associates who live and work in these particular communities.”
Hexion’s facility in Lakeland, Fla., donated two large drums of isopropyl alcohol to the local Polk County Sheriff’s office, which in turn sent the chemical compound to another manufacturer to make much-needed disinfectant. The company’s research and development center for composites in China donated masks to local hospitals.
In western Australia, Hexion has a joint venture with another company. “They decided to take some idle mixing equipment, put in some piping and hook up storage tanks to the mixer to make commercial quantities of hand sanitizer with a recipe from the World Health Organization,” says Paul Barletta, executive vice president of operations. The facility plans to make thousands of kilotons of hand sanitizer for donation and sale.
In addition, several facilities around the world have made hand sanitizer in their labs for employees to use and to donate to hospitals. As resin suppliers, the plants have enough of the basic chemicals – such as isopropyl alcohol, glycerin and gel – to make small batches for use in their immediate communities.
Hexion’s contributions have helped others, but they also provide a lift for the company’s employees. “It’s been a big morale booster for our associates,” says Knight. “We have people working from home and our plants are running, but this is something they can rally around.”
Fabricating Face Shields
One of the most common PPE items being made by composites companies around the world are face shields. TRB Lightweight Structures in Huntingdon, England, redeployed personnel and machinery that normally create advanced composite components for electric vehicles to produce 1,000 reusable face visors a day. Cincinnati-based A&P Technology Inc. has made more than 15,000 face shields.
“We saw the need in industry to help protect our frontline healthcare workers,” says Molly Dingeldein, marketing manager for A&P Technology. “Our shop and fabrication area can quickly turn around products, so we thought it would be a good thing to do.” Initially, the company made the polycarbonate face shields on its high-capacity milling equipment for family members and friends of employees who work in healthcare. Then, it expanded to provide masks to local hospitals, fire departments and nursing homes. It also partnered with a local organization called May We Help to seek out recipients who need face shields.
While A&P Technology has remained open as an essential business during the coronavirus pandemic, face shield production has helped keep employees busy. “Some of our production has been stopped or suspended in the aerospace area,” says Dingeldein. “Employees in those production cells have been helping with the fabrication of face shields.”
Miles Fiberglass & Composites has also diverted some employees to the production of face shields. “We were successful During the coronavirus pandemic, personal protective equipment is critical for workers in a variety of industries. This employee of a wastewater treatment plant uses a face shield made by Miles Fiberglass & Composites.
“We were successful t receiving a Paycheck Protection Program loan, so we kept our employees [during the pandemic]. But our sales had fallen off a bit, so we had extra labor,” says Miles-Olund. “We decided to use the extra labor to produce shields for material cost only. It was a way we could help out with little retooling.”
The company used open source face shield directions from the University of Wisconsin’s Makerspace to create the disposable shields made from plastic, foam and an elastic strap. Miles Fiberglass & Composites has supplied face shields to a variety of organizations, including a wastewater treatment plant, an ophthalmologist, a medical center in Connecticut and Parrot Creek Ranch, a long-term residential treatment program for adolescent boys. “The community has been so supportive helping us contact organizations and get the word out,” says Miles-Olund.
Making a Difference
As the country grapples with the ongoing pandemic and how to safely return to life’s daily activities, composites companies continue to think of ways they can help. Recently, A&P designed anti-abrasive sneeze guards that companies can place on desks and counters to protect staff and customers from germs. The ¼-inch thick acrylic sneeze guards, which the company branded IgGY Guards in a nod to immunoglobulin G (IgG) antibodies, are available in 46 x 36-inch rectangular sheets or 31 x 44.5-inch curved sheets, as well as custom sizes.
No matter the product, from simple face masks to large isolation booths, employees appreciate being able to contribute during these unprecedented times. “This pandemic has created a lot of stress and uncertainty. People feel powerless and don’t know what they can do about it,” says Bridge. “If you can give employees something tangible, where they can pitch in and help a local hospital or other organization, that helps take some of the stress away. They are making a difference where they can.”
Thank you notes and emails, particularly from frontline healthcare professionals, confirm that composites companies are indeed making a difference. One registered nurse from Good Samaritan Hospital in Cincinnati summed it up in a note to A&P Technology: “I have so much gratitude to your company for deciding that you wanted to help in the battle we healthcare workers are fighting against the pandemic. Your efforts make us feel a little safer and protected.”
SUBSCRIBE TO CM MAGAZINE
Composites Manufacturing Magazine is the official publication of the American Composites Manufacturers Association. Subscribe to get a free annual subscription to Composites Manufacturing Magazine and receive composites industry insights you can’t get anywhere else.