
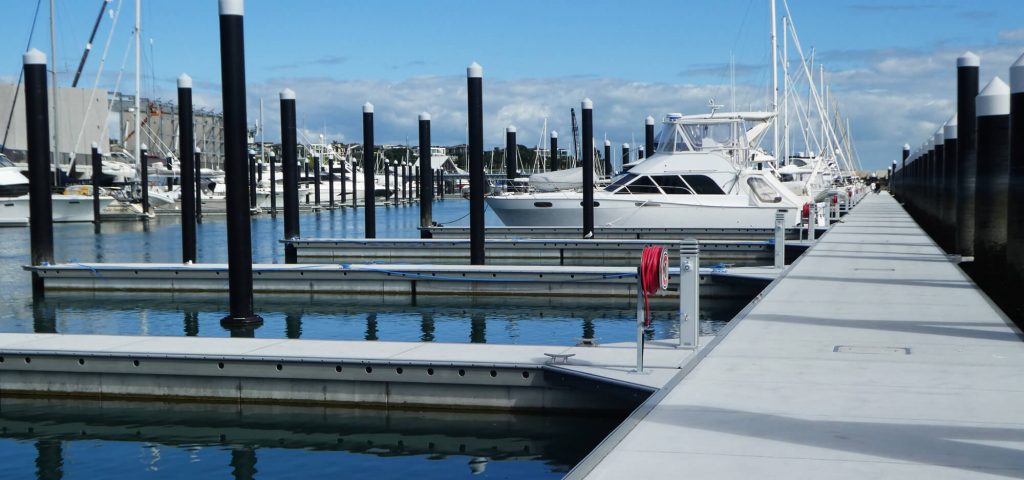
GFRP Takes Center Stage in Floating Docks
Bellingham Marine, headquartered in Newport Beach, Calif., recently installed its first fully GFRP-reinforced Unifloat® concrete dock system in a New Zealand marina. The docks, which feature GFRP thru-rods, rebar and beams, are lighter, stronger, easier to maintain and more environmentally friendly than steel and timber-reinforced ones. With an expected lifespan of 100 years or more, they also offer extreme durability.
“Most floating docks use treated timber for the walers and steel bolts to hold them onto the floats, which are reinforced with steel rebar,” says Pete Renshaw, business development director at Pultron Composites Ltd. in Auckland, New Zealand. “All of these are subject to deterioration over time and limit the lifespan of the structure.”
The dock system is the culmination of a decade-long collaboration between Bellingham Marine and Pultron Composites to replace timber and steel dock reinforcements with composites. The companies first tackled the thru-rods, which attach floating concrete sections to walers (structural beams mounted to the deck). To develop the thru-rods, which were introduced in 2015, Pultron relied on its experience producing GFRP rock bolts for tunnels and mine reinforcement and its work in the sports and recreation industry.
“We knew that the tie rods would be subjected to constant wave movement affecting the dock system, so we used some of our know-how from [GFRP] trampoline rods that we developed, which have high flexural fatigue resistance,” says Renshaw.
While the GFRP thru-rods have twice the tensile strength of steel, they have a low tensile modulus. This allows them to stretch and contract and maintain tension.
“This has proven to be a big advantage as it saves a lot of maintenance,” says Renshaw. “As the timber dries, it can shrink enough for the steel bolts to become loose, but the extra stretch in the GFRP bolts accommodates this shrinkage so they do not come loose. Much less retightening is now required.”
Pultron Composites pultrudes 20-millimeter-diameter thru-rods using corrosion-resistant ECR glass rovings and a proprietary resin system in lengths up to 12 meters. After fabrication, a purpose-built CNC grinding machine turns the smooth rods into threaded bolts.
“Rather than cutting the thread, as is normally done for steel bolts, our threads are ground into the surface using profiled diamond grinding wheels,” says Renshaw. The nuts are injection-molded from glass-filled nylon by Lane Plastics, another Auckland company.
After developing thru-rods, Bellingham began efforts to replace the steel rebar in concrete floats with Mateenbar™, a GFRP rebar developed by Pultron and manufactured by Mateenbar Ltd. Although Mateenbar had been used in more than a thousand infrastructure projects, including roads, bridges, tunnels, seawalls and aluminum smelters, concrete floats were new territory. Consequently, Bellingham trialed them in marinas in Australia and Cyprus before introducing them commercially in 2018.
The switch to Mateenbar increases float lifespan considerably. “The American Concrete Institute developed an accelerated test method to determine deterioration of GFRP rebar,” says Renshaw. “This test indicated that we should expect a strength retention of around 96% after 100 years.” At 25% the weight of traditional rebar, Mateenbar also reduces shipping costs and eases installation.
The GFRP thru-rods and Mateenbar have been standard in Bellingham’s Unifloat concrete dock system in New Zealand for the past three years, including more than a dozen projects. Last year, Bellingham introduced the final GFRP reinforcement into its floating concrete dock system – the waler.
Traditionally built with treated timber, walers are mounted to the side of multiple concrete floats and fasten them together. Pultron manufactures the walers with a pultrusion process similar to thru-rod production. However, in addition to the ECR glass rovings and polyester resin, the waler has a continuous filament mat for transverse strength and a surface veil that provides a smooth finish and additional UV protection.
Measuring 12 meters long and weighing 330 pounds, the waler is the largest, heaviest profile that Pultron has made.
“This created some challenges. For example, the waler required so many rovings that we had to extend the roving bay, which feeds glass fibers into the pultrusion machines, making it both longer and taller to increase the capacity by 30%,” says Renshaw.
Pultron also had to modify its handling processes. While other products could easily be moved by one or two people after production, the waler required installation of a moveable gantry.
“When the factory was built over 35 years ago, the longest product that Pultron regularly made was much smaller,” says Renshaw. “Trying to maneuver a 12-meter-long waler weighing 150 kilograms around a factory that was never built for such large, heavy profiles is not easy.” Pultron is currently expanding its factory to increase capacity, improve efficiencies and allow for easier handling of such large sections.
The first installation of the GFRP-reinforced Unifloat concrete dock system added 100 new berths and a fuel jetty in Half Moon Bay Marina in Auckland. Bellingham will soon begin installation on the first Unifloat dock system in the United States to systematically refurbish and rearrange 2,400 traditionally reinforced berths in Dana Point Harbor, Calif., while the marina remains open. Sustainability was a selling point for the California marina.
“FRP walers are considered to preserve water quality and ensure no treated timber [chemicals] leaches into the water,” says Chris Lamont, general manager of Bellingham Marine New Zealand. “Dana Point has large sea lion populations, and this was very important to the project to ensure that they and other marine life were not compromised.”
Melissa O’Leary is a freelance writer in Cleveland. Email comments to melissa@good4you.org.
Half Moon Bay Marina in Auckland, New Zealand, added 100 new berths and a fuel jetty made with the Unifloat® GFRP-reinforced concrete dock system.
Photo Credit: Bellingham Marine
Crews install the Unifloat® concrete dock system.
Photo Credit: Bellingham Marine
SUBSCRIBE TO CM MAGAZINE
Composites Manufacturing Magazine is the official publication of the American Composites Manufacturers Association. Subscribe to get a free annual subscription to Composites Manufacturing Magazine and receive composites industry insights you can’t get anywhere else.