The properties of composite materials and their manufacturing process usually drive the selection of FRP composite materials. The lamina properties of FRPs, including the properties of core materials (if involved), are calculated, and the material safety factors and design values are determined. Manufacturing methods suitable for the proposed structure should be selected to achieve high fiber content and to enhance the strength and stiffness of the material. Designers also can take advantage of the fact that composite materials are anisotropic, so they can be designed and manufactured with properties varying in different directions to suit the application needs, dependent on load paths.
During the material selection process, designers should consider numerous factors, including corrosion, weathering and the material safety factor. With regard to safety factor, uncertainties due to a combination of effects corresponding to various knock-downs (under temperature, moisture, sustained stress/creep and fatigue) should be taken into account. In addition, uncertainties regarding targeted material design properties should be considered. It is extremely important to note that proper selection of the manufacturing process, as well as the constituent materials (resins, fibers, additives) for a tailor-made composite structure, are essential to meet minimum design and performance requirements.
Define the Structural Concepts
The next step is to define the structural concepts of the proposed FRP structure. Usually, a minimum of three important aspects should be considered: 1) use of a limited number of connections, 2) optimal design under water or barge impact loads and leakage flows and 3) uniform load transfer over the entire structure. The design includes guiding principles for the structural concepts, description and calculation of different options, such as sandwich structure versus box beam. Then, the most suitable option of optimal design is selected to meet the strength and deflection requirements.
Take Deflection Requirements into Account
In some cases, the maximum deflection requirement influences the design of a composite hydraulic structure since the stiffness of the GFRP composite is low. To meet the stiffness requirement, CFRP can be used at a different cost scenario, recognizing that the potential for galvanic corrosion exists when in direct contact with steel.
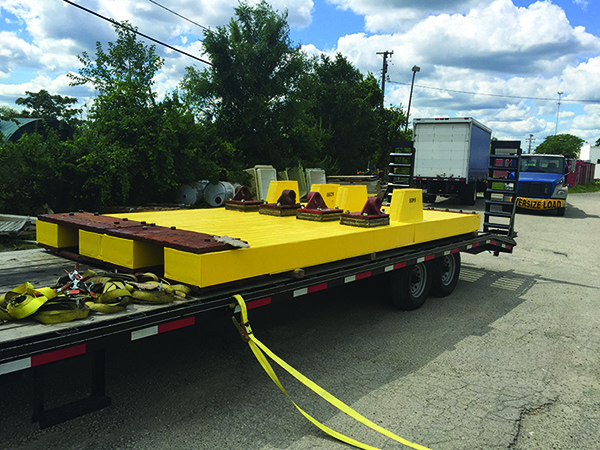
The wicket gates shown here prior to transport were installed on the Peoria Lock & Dam on the Illinois river in 2015. The 10 x 12-foot panels feature a vinyl ester resin and more than 30 layers of fiberglass fabric, including 0/90 degree and +45 degree fabrics. Photo credit: Composite Advantage
Perform a Cost Comparison
The cost comparison should be made among different design options. A life cycle cost analysis should be used when designing with composites as an alternative to conventional materials because FRP offers longer service life and lower maintenance costs, but at a higher initial cost in some scenarios and at a competitive price in other cases, such as wicket gates.
These five considerations only begin to address the budding hydraulic structures market. Educating owners and designers about composites – including specification developments and training fabricators of composite systems – are real challenges facing the market. Even so, the future is promising, provided that high-quality workmanship and installation procedures are ensured. Based on limited in-service data, it is safe to conclude that GFRP systems for hydraulic structures are resulting in longer service life, lower initial costs (in some cases) and reduced life-cycle costs with enhanced structural performance.