CM: How will GM’s strategy to sell only zero emissions vehicle by 2035 impact the design and engineering requirements for future vehicles?
Voss: The high-level goal is to give the customer the same experience, whether it’s an electric or conventional power train vehicle. You want the electric vehicles to be transparent to the consumer from a range perspective, usability perspective and safety perspective.
The main challenge with electrification is it requires a big battery. You’ve got this huge assembly that now needs to be packaged into the vehicle. You need to engineer the vehicle so it’s safe in an impact or crash scenario, but also design it so the consumer’s feet are comfortable on the floor and the seating position is comfortable. You’ve got to take advantage of spaces like the frunk. From a vehicle integration perspective, we now have these new features that we can engineer. Part integration and mass present opportunities where composites can really come into play.
Now, take everything I just walked through and optimize it so it meets our business targets. That’s the challenge for material systems, and that’s how it impacts us in the design and engineering community on a daily basis.
CM: Given GM’s goal to achieve at least 50% sustainable material content by 2030, what are the key criteria to be used to evaluate the sustainability of materials?
Voss: We define sustainability as reducing dependence on nonrenewable resources or minimizing disruption to the environment or key natural resources. The CarbonPro includes two parts – front stack pocket reinforcements – that are made 100% from recycled thermoplastic materials. We engineered the product to take advantage of that material system and to incorporate recycled materials directly into the product. Recyclable materials could be from end-of-life or from the manufacturing process. There is a direct way we can reuse materials and make them renewable in the product cycle.
Aluminum and steel represent the Holy Grail: They are recyclable and have an infrastructure in place to reclaim those materials from vehicles. Those are the steps that composites need to take.
CM: How does the zero emissions goal and the need to increase sustainable content translate into the selection of materials for future vehicles?
Voss: It’s another aspect of the decision matrix, which includes everything from the strength of the material to how you form it and its thermal properties and cost. Obviously, based on our vision statement, it’s a priority. I can’t talk about how we internally balance different parts of the matrix, but it’s definitely a focus point as we move forward.
CM: Is there anything else you think companies in the composites industry should know about GM and its strategic goals for the future?
Voss: Think back five or 10 years ago. Vehicles were constructed in the same way, at a high level, as they had been for the past 80 years. It’s only been within the past decade that the industry has shifted. And as it shifts, that presents opportunities.
Vehicles are put together in new ways. We are using new materials, new parts and components and new assembly strategies. For companies that do their work and understand their materials and the advantages they bring, there is more opportunity than ever for them to apply the materials on vehicles. I’d encourage companies to reach out to engineering here at GM and explore those opportunities.
Susan Keen Flynn is managing editor of Composites Manufacturing magazine. Email comments to sflynn@keenconcepts.net.
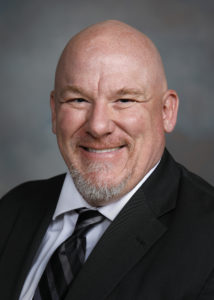
Mark Voss, who joined GM in 2000, has been at the forefront of many of the company’s applications of carbon fiber, including composite body panels for the 2014 Corvette Stingray and the CarbonPro™ box in the 2019 GMC Sierra.
Photo Credit: General Motors Company
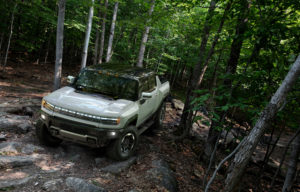
The GMC HUMMER EV pickup, which will be available in the fall, is the first all-electric supertruck.
Photo Credit: General Motors Company
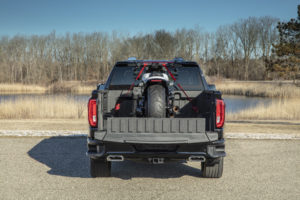
The 2019 Sierra Denali features the CarbonPro™ truck bed, which weighs 25% less than a traditional steel bed and removes approximately 60 pounds from the vehicle mass.
Photo Credit: General Motors Company